A brief analysis of the quenching deformation analysis of the die of the card cutter and the improvement of the water immersion quenching process of high-frequency induction quenching equipment
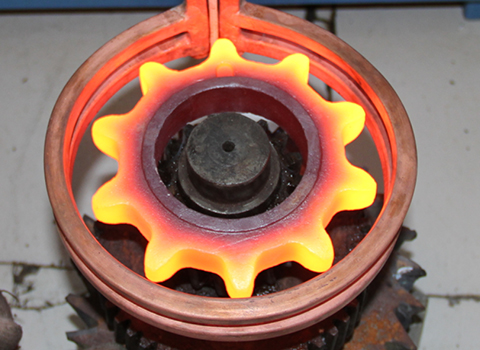
The card cutter die is a mold for processing and manufacturing business cards and paper cards. The workpiece material is 45 steel. The hardness of the die of the card cutter is required to be 50-55HRC, and the assembly gap of the convex and die after processing is required to be 0.01-0.02mm. The original process of the card cutting die adopts the overall quenching process. During production, it was found that the deformation of the concave mold after treatment reached 0.10~20mm, which brought great difficulties to the grinding and repair of the mold. The grinding volume was large, labor-consuming and time-consuming, the production efficiency was low, and the cost was increased. Analysis of the working part and stress characteristics of the die of the card cutter shows that the main working part of the die is the cutting edge, and the depth of the cutting edge is 3mm. Therefore, the hardened layer of the workpiece does not need to be too deep, and it is enough to ensure that the cutting edge is quenched thoroughly. Surface hardening by high-frequency induction quenching equipment can meet the requirements. On the other hand, using high-frequency induction quenching equipment for quenching can significantly reduce the shrinkage and deformation of the die, which can solve the problem of workpiece deformation out of tolerance. During the test, it was found that because the cutting edge of the mold is thin and quenching is performed after local heating, the workpiece will cool down quickly and be difficult to harden. The hardness will not meet the requirements and the strength of the mold will be insufficient. If the inductor is used for water spray quenching, the mold cooling will be uneven, the workpiece hardness will be uneven, and it will not meet the technical requirements. If external spray quenching cooling is used, precise operation is the key to the technology. If a computer bucket is not used, soft spots will appear in some parts, and the effect is not ideal, so it is not used. The high-frequency water immersion heating and quenching process solves the above problems well. This process uses a mold notch profiling (rectangular) sensor (made of 10mm pure copper tube). The distance between the sensor and the mold edge is 4mm. After the die of the card cutter is immersed in water, it is heated to 880-900°C for a time of 1s. It is then quenched by water immersion when the power is turned off. The hardness of the cutting edge is >55HRC, and the amount of shrinkage deformation is <0.04mm. After quenching the die, temper it in a nitrate salt bath at 220°C After the 45 steel card cutter die adopts the water quenching process of high-frequency induction quenching equipment, the workpiece quality is excellent and the deformation is small (<0.04mm), which meets the production technical requirements and the production runs well.
Related News